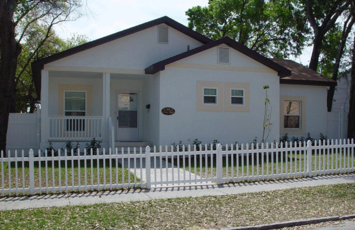
If the predictions are accurate, America will have to house some 100 million more people by 2040 to mid-century than is now the case. Despite the current round of foreclosures and rising apartment vacancy, over the long term the demand for humane, affordable, sustainable housing is going to escalate dramatically in the coming years.
In this recessionary time, it may be tempting to ignore the coming boost in housing demand. Yet eventually growth will pick up and the housing market will become re-invigorated. Nonetheless, the problem of meeting the demand for affordable housing will remain. For now, the federal government is trying to help state and local governments acquire, renovate and sell foreclosed properties, and individual homeowners to reduce their mortgage payments to 31 percent of their income. Federal efforts are also being aimed at increasing funds to redevelop public housing and at giving first-time homebuyers an $8,000 tax credit.
But these are short-term measures. Others, with more lasting impact, may be more effective. One will be the size of houses. Although some may still choose to build large lot homes and McMansions, the longer-term trend will be for somewhat more compact houses. Contrary to the visions of some urban boosters, Americans will continue to favor single family homes over apartments. But these houses seem likely to trend back to the more traditional, modest scale. Between 2006 and 2007, after years of expanding, the size of a median single-family house actually decreased slightly.
Another critical element of a housing solution lies in building workforce housing close to the workplace. For years, many moderate income Americans have been forced to “drive ‘til they qualify.” Throughout the nation’s metropolitan areas, teachers, police officers, firefighters, salesclerks, municipal workers, and young people, among others, are being elbowed out of the local housing market. In a recent survey conducted by the Urban Land Institute in cooperation with Harris interactive, of the 110 larger firms (over 100 employees) surveyed, fifty-five percent reported a lack of affordable housing nearby, sixty-seven percent of the workers interviewed (who earned less than $50,000 per year) said they would move closer to work if more housing in their price range were available, and fifty-eight percent of the companies reported having lost employees due in part to long commute times.
For most Americans, particularly between ages 30 and 70, the demand for affordable homes near workplaces will be paramount. In some areas, there may also be greater demand for apartments, even though these too are suffering due to the recession.
Many zoning and building codes are obsolete and need to be updated, because as written they restrict the construction of low and moderate income housing and segregate residential, retail, and industrial/commercial land uses. Changing zoning to permit and provide incentives for mixed use development, more intense land uses, and higher density development would make workforce housing more affordable.
The steps above do not apply only to city living. Through good design, suburban living can be made slightly more compact without sacrificing quality of life. Accessory buildings can often be added on a lot, “granny flats” can be built, large old single family homes can be converted into duplexes, empty spaces could be filled in, and other steps can be taken to meet the need for more housing when that need materializes.
But perhaps the biggest gains can come by using innovative approaches to expanding housing. One novel idea that has begun to emerge is to use old shipping containers that have been transformed into building blocks for home-building materials. Actually, one can hardly call the idea novel, because shipping crates have been used in construction for thousands of years. But today, the old practice is being revived with entrepreneurial, innovative, outside-the-box thinking.
These reconfigured containers have the advantages of being more economical and durable than conventional materials, speedier to construct, highly customizable, fire-, termite-, water-, and earthquake/hurricane-resistant, strong, safe and green, with a lower carbon footprint. Hence the name of one of the companies working in this field, one with which I am associated, SG Blocks LLC (SG stands for “safe and green”). As the company puts it, “We are in the business of converting instruments of trade into instruments of construction.”
Shipping containers are big: each weighs 9,000 pounds and measures 8 feet wide by 40 feet long by 9 feet tall. Hundreds and thousands of them are sitting empty in ports around the country. What possible use could they be, one may wonder, in building a new residential or office complex?
Consider, therefore, that these steel-on-steel containers, when used as re-fabricated “blocks,” are stronger than conventional house framing. They can be cut, fabricated, re-modeled, and turned into a basic home structure for approximately $25-$27 a square foot. Stevan Armstrong, COO of SG Blocks, has pointed out that multi-family mid-rise units built with containers cost 10 to 15 percent less than typical “stick frame” houses. When appropriate coatings are installed, says Dan Rosenthal, a principal with the Lawrence Group, “we have an envelope that reflects about 95 percent of outside radiation, resists the loss of interior heat, provides an excellent air infiltration barrier and does not allow water to migrate in. Because of the superior roof structure, it is easier to incorporate ‘green’ roof systems.”
Using shipping containers also saves energy on the front end. It takes 6,481 kilowatt-hours to make a ton of steel from virgin materials, 9,000 kilowatt hours of energy to melt down a container, but only 400 kilowatt-hours of energy to convert shipping containers into SG Blocks.
The possibilities for utilizing this type of construction – infill housing in urban and suburban communities, new construction for residential, commercial, industrial and retail buildings, single- and multi-family homes – are practically limitless. From a design perspective, SG Blocks claims that their modified containers “can be used to build virtually any style of construction, from traditional to modern and all in between...from traditional Main Street to ultra-contemporary.” In short, they can provide people with an opportunity for ownership and economic mobility in a decent community environment.
To cite a few examples:
- A continuing care community for seniors on the historic Mission San Luis Rey grounds in Oceanside, CA, 340,000 square feet with 450 SG Blocks, is going up.
- In Salt Lake City, the first mid-rise container building is being planned for downtown; it will be called City Center Lofts, with eight units and a ground level art gallery.
- In Ft. Collins, CO, discussions are being held about creating “block” homes for 500 families as part of the city’s Homeless Shelter Program.
- John Knott, the guiding light in the Noisette Community in North Charleston, SC, wants to build a six- to eight-story “container” building, retail on the first floor with residential units above, topped with a green roof. He proposes using ninety prison re-entry men to do the construction.
- Work is in process on a three- to four-story student housing and recreational mixed use facility at Lubbock Christian University in Texas.
- In Panama, “blocks” are being used to build four buildings that will house community and education centers for the U.S. Southern Command.
- Attached to the top of this article is a photo of a house built with SGBlocks in St. Petersburg, FL.
Demography is destiny, as has been said so many times. With 100 million more people in the pipeline, we have to find humane, innovative, affordable ways to house them and provide them with opportunity for advancement. Salvaging empty shipping containers to address this problem is only one step, but a most interesting one that is well worth the trying.
William H. Hudnut III, former Member of Congress and sixteen-year Mayor of Indianapolis, is the principal in his firm, Bill Hudnut Consultants LLC, and an associate of SG Blocks LLC. His email address is: bhudnut3@gmail.com.
Shipping
Many zoning and building codes are obsolete and need to be updated, because as written they restrict the construction of low and moderate income housing and segregate residential, retail, and industrial/commercial land uses. Changing zoning to car shipping permit and provide incentives for mixed use development, more intense land uses, and higher density development would make workforce housing more affordable.
Housing!!!!!!!!!!!!
Home construction has become one of the biggest home and office construction trends globally. Shipping container construction has become popular for not only homes, but for offices, hotels, student housing, safe rooms, and emergency shelters.THanks for sharing this information.
True
Very true...Its becoming increasingly difficult to construct homes,people are more keen on purchasing accommodation
I agree with this. mailing
I agree with this. mailing fulfilment services
Shipping Container Home
Shipping Container Home construction has become one of the biggest home and office construction trends globally. Since 2005 shipping containers began to appear in many news stories in the U.S., Canada, UK, Netherlands, China, Australia, New Zealand, and much of Europe. Shipping container construction has become popular for not only homes, but for offices, hotels, student housing, safe rooms, and emergency shelters.
SG Blocks
Many of you bring up good points that we have had to address through the development of our building system and wanted to elaborate on a few. Shipping containers are just the building blocks or the skeleton of a building. We like to say, it’s the Intel inside, using a computer term. For the majority of the houses built using this system, people will not even know that it was a shipping container unless you tell them. If you want an industrial look you can leave the corrugated metal exposed but if you want a traditional look you can use any conventional siding material you want including brick and other masonry products. Many attempts to use containers in Europe have focused on the industrial or minimalist look. It’s eye catching and different but limiting and looks sometimes like storage boxes painted to look pretty. Some U.S. based “container architects” are also sticking to that look. With rising awareness of the environmental impacts of construction, the market has an increasing interest in recycled products as well as the recycled look. SG Blocks has mainstreamed the building system so you can get the aesthetics you want while maintaining compatibility with other traditional building materials. This allows the owner to utilize many traditional finishes inside and out while receiving the advantages of robust, steel framed construction at, or below the costs of conventional stick built systems. Like most building designs, it ultimately comes down to owner’s goals and how the architect designs the structure to meet them.
The room sizes are typical dimensions allowing for a variety of layouts. The home in the picture, has bedrooms that are 10’x12’ and the kitchen and living spaces are open with overall dimensions close to 18 feet. The 8 foot x 40 foot modular dimension is no more limiting than standard conventional framing. We don’t let dimensional lumber or standard size concrete blocks limit our spaces and SG Blocks are the same. Ceiling heights are at least 8 foot in the bedrooms and 9 feet in the living space which is normal for similar style housing in this price range.
The insulations used include the latest technologies available which means they are superior to the standard batt insulation that is used in virtually every home in the US. In addition, the walls are thinner not thicker. The combination of modern insulation materials, moisture resistant framing and very tight building envelop reduces the chances for mold growth and other moisture issues so common in traditional construction.
The system is termite proof, stronger than standard wood framing, durable, fire resistive, meets or exceed all code requirements and is cost effective. It has a smaller carbon footprint than conventional stick built homes and it helps solve a tough problem of what to do with the excess containers clogging our ports. It is a better alternative than site built wood frame in many situations. It is not a panacea, it’s not meant to completely replace other approaches to construction. It’s a viable alternative that solves some pressing problems with traditional site built wood framed housing.
The house pictured in the article was built because a hurricane destroyed the previous home. To build a home this strong, out of new steel, that is hurricane resistant, just wouldn’t make sense economically or environmentally. Unless using recycled steel materials, such as shipping containers, it is typically cost prohibitive for the average consumer to build a home as strong as a shipping container home. Exceeding the structural limits of conventional stick built homes has proven to be extremely valuable to many people including those in areas susceptible to inclement weather. Residents in many neighborhoods such as this, can’t afford the luxury of building with materials stronger than typical dimensional lumber making this option not only cost effective but safe.
An additional comment
My article may have been deficient in not explaining thoroughly that SGBlocks are open, not closed. Their steel framework blocks can be assembled in any number of patterns. We're talking about an “opened” up box that creates larger spaces. When we build homes out of lumber people do not assume it’s a tree; they assume the tree has been milled and sawed and created to serve a need. Man or woman do not limit themselves to just a tree….or to a container box.
Appreciate all the comments! Thank you.
I don't understand the
I don't understand the objection to shipping containers. Several super-cool architect design houses for the hip and trendy have been made out of them, so I don't see how you say they are crass and inhumane. The hostility seems rather unwarranted.
The dimensions of a container are not the limiting factor as you can assemble multiple of them. It should be possible to re-fabricate them in a factory and ship them to the site for assembly as with modular homes. This could be an interesting variant on the idea of modern pre-fab, with the added twist of a reused shell. In the US as well, modern pre-fab has tended to be fairly expensive, but this is an industry that is clearly not yet operating at scale. In the US, unlike the UK, pro-growth planning and zoning makes it easier, particularly in many inner cities where land prices are simply not an issue.
Maybe this will work and maybe it won't, but it's worth checking out and giving a try.
Agreed
As an architect currently working on a shipping container project, I agree with Aaron that this idea is definitely worth exploring. The concerns that others mention are noted, yet definitely solvable.
Our project is not a large scale project for housing multitudes, but is in fact a single-family home made from 6 attached ISBU modules. If we come up with a design humane enough to be a (small) second home, surely it could have scalable applications.
The 8' width is not a limiting factor to room size, just a module for combining together, and so far we are having a blast with the design.
Check out our initial ideas and let us know what you think:
Shipping Containers and Alpacas
Andrew Wilson
[1016] Architecture Inc.
Blog: Inside the Brackets
Is it a Home, Architecture, Recycling or a Step Backward?
In a world where we throw too much away without thinking; re-using obsolete shipping containers is a step in the right direction.
But is using them to live in the right solution?
It may well be profitable for SG Blocks LLC and make them feel good; that they are doing their bit for saving energy and the environment. However I'd need to spend some time in one to be convinced
The picture at the top of the article looks like the American Dream with the picket fence and front porch and perhaps the clever coatings Will Hudnutt mentions will go some way to address the drawbacks of living in a tin can.
Even so I have a number of questions I'd need answering even before I'd suggest using containers for a convicted prisoner:
@ Ventilation? Containers are perfect for keeping goods dry for shipping, but humans have a nasty habit of breathing and steel walls and roof will need more than just covering to prevent condensation.
@ Insulation? If you've ever opened a container in an outdoor shipping dock you'll know it has a great ability to move to extremes of temperature: Hands stick to frozen walls or cook your own pizza depending on the weather.
@ Windows and Doors? S&G may well have developed their own supply of windows suited to fitting in to a container profile, sealing reliably and providing great thermal performance, if not it won't be a great place to live.
@ Wall thickness? The classic container profile is corrugated for extra strength so, to get decent aesthetics you need to clad both sides to hide the fact that you want someone to live in a crate. If you also want to insulate and achieve thermal performance the wall will get thicker and the rooms get smaller. The good thing about this is that it will reduce the noise of living in a steel drum.
I'd be willing to guess that the S&G team have tried to address all these issues and if they are successfully selling their products they must have answered them quite well. If not the business will either be short lived or the occupiers will be so poor that their voices do not count.
Modular buildings were rejected in the 20th Century because they were seen as cheap utilitarian commodities which provided a poor quality of life. Many modular system designers have shown over the last 10 years that great architecture can be created, achieving previously unimaginable levels of building design, speed, quality and performance.
The conservative world of construction has resisted the move towards 'manufactured' buildings using the argument that they will be ugly, industrial and all look the same.
In S&G they may have found a business that justifies their resistance to change, but I hope S&G can prove me wrong.
“S&G are in the business of converting instruments of trade into instruments of construction.”
"Total Flow are in the business of creating the best homeowner experience at the least capital and environmental cost."
Tim
Total Flow Limited
+44 7870 274756
http://www.linkedin.com/in/tghall
Twitter: TG_Hall
For our services visit: www.totalflow.co.uk
For our ideas visit: www.totalflow.co.uk/blog