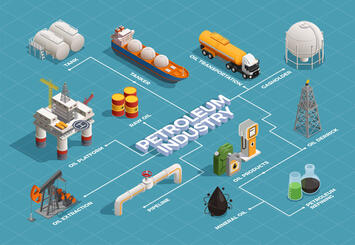
The hydrocarbon processing industry, i.e., refineries, has a rich history of discovery, challenges, breakthroughs, trial and error, collaboration, and success. Looking back a little more than 100 years, it’s easy to see how civilization has benefited from more than 250 leading-edge, hydrocarbon processing licensed refining technologies used by the more than 700 refineries worldwide that service the demands of the 8 billion living on earth with more than 6,000 products made from the oil derivatives manufactured out of raw crude oil at refineries. None of these products were available to society before 1900.
If it were not for the demands of society, it’s easy to understand that there would be no need whatsoever for the supply of crude oil to refineries, to be manufactured into usable products if there was no demand for those products. As the public remains unwilling to be mandated and regulated into an inferior lifestyle like our predecessors just a few hundred years ago, we have been witnessing shortages and inflation of most everything these days.
With the world enthralled with the Environmental, Social and Governance (ESG) movement to divest in fossil fuels and plastic i.e., bottles, plates, and utensils and with no known replacement in the foreseeable future for the crude oil used in the hydrocarbon processing industry, i.e., refineries, let’s review some of the inventions that may be excluded from our lifestyles in the future. We’ll do a review, in layman’s terms, on the origins of the modern refining and petrochemicals industries that supports todays demands for polyethylene, synthetic fibers, resins, and jet engines:
- The hydrocarbon processing industry continued to evolve during the 1930s. Starting with the discovery of kerosene, the construction of new refineries around the world, the production of the first synthetic plastics, and the rise of the internal combustion engine (ICE), oil demand’s exponential growth during and after World War I (WWI) and how thermal cracking evolved in refining processing.
- Around the timeframe (circa 1938), the alkylation process was commercialized in the U.S. The process produced high-octane aviation fuel, which saw significant demand increase during World War 2 (WW2). The process was then used in the 1950s to produce blending components for automotive fuel.
- In 1939, the first commercial-scale polyethylene plant went into operation on an industrial scale. Within the next few years, many polyethylene plants went into operation, primarily to aide in the allied war effort. polyethylene was used extensively as insulating material for radar cables during WW2. The material was lightweight, which enabled Britain to install radar in their fighter planes, providing a significant technical advantage in long-distance air warfare. Due to this wartime advantage, the production of polyethylene for insulated cabling was highly secretive. It was not until post WW2 that the production of polyethylene was commercialized. Within several years, PE production capacity significantly increased and would later become the world’s most used thermoplastic.
- Several new chemical discoveries took place in the 1930s that have provided the global population with new products to improve standards of living. These included the discovery and production of polystyrene, polyepoxide, nylon, polyester, and neoprene.
- Although polystyrene was discovered in the late 1830s, styrene—which would lead to the production of polystyrene—would not be commercialized for nearly 100 years. Styrene production increased significantly in both Germany and in the U.S. during WW2 to produce synthetic rubbers to aide in the war effort. In the late 1930s, Dow Chemical created foam polystyrene which expanded approximately 40 times in size. Dow would later commercialize this discovery as expanded polystyrene, better known and marketed under the name Styrofoam.
- After the discovery of neoprene in 1931 for many applications (construction, automotive, medical equipment, fabrics, electrical equipment, textiles, among others) efforts were directed to producing synthetic fibers. By the mid-1930s, Nylon first became a household product as women’s hosiery, later being used in the U.S. war effort to produce parachutes and tents. Over the next several decades, nylon would be used extensively as a combined fabric in fashion and apparel, as well as in several industrial applications—the global nylon industry market size is forecast to reach more than $46 billion by the late 2020s.
- Research also led to the discovery of polyester in the early 1930s. However, the discovery of nylon pushed additional research on polyester to the backburner. It was not until the late 1930s that work on synthetic fibers would eventually lead to the development of polyethylene terephthalate (PET) in 1941. In the early 1970s, PET began to be used in the production of plastic bottles, and today, PET is the fourth most produced polymer after PE, polypropylene, and polyvinyl chloride.
- The DuPont company was not finished with major polymer discoveries of the 1930s. Researching chlorofluorocarbon refrigerants to find a better way to refrigerate food. Further investigation found the substance to be heat resistant and had a low surface friction. DuPont polymer scientists determined that the tetrafluoroethylene gas polymerized to produce the material, which DuPont would later market under the name Teflon.
- In 1936, Monsanto Chemical Co., produced melamine formaldehyde by polymerizing formaldehyde with melamine. This new substance was a thermosetting plastic that was very good at maintaining strength and shape. Melamine resins were used for many different applications, including in utensils, plates, furniture, cups, bowls, laminates, toilet seats, automotive and epoxy coatings, among others. Polymethyl methacrylate (PMMA) is a clear thermoplastic resin that is more transparent than glass and 6x–7x more resistant to breakage than glass. PMMA is also known as acrylic, acrylic glass, perspex, or plexiglass, as well as by the trade names and brands Crylux, Plexiglas, Acrylite, Astariglas, Lucite, Perclax, and Perspex, among several others. This plastic is often used in sheet form as a lightweight or shatter-resistant alternative to glass. It can also be used as a casting resin, in inks and coatings, and for many other purposes.
- Polymethyl methacrylate (PMMA) is commonly used for prosthetic dental applications, including the fabrication of artificial teeth, denture bases, dentures, obturators, orthodontic retainers, temporary or provisional crowns, and for the repair of dental prostheses.
Read the rest at CFACT.
Ron Stein is an engineer who, drawing upon 25 years of project management and business development experience, launched PTS Advance in 1995. He is an author, engineer, and energy expert who writes frequently on issues of energy and economics.
Photo credit: courtesy CFACT